Window construction
Substructure insulating profile (UDP)
The floor recess for doors and floor-to-ceiling elements places high demands on substructure insulating profiles. These are met with CFeco.
The COMPACFOAM-The UDP substructure insulating profile combines strength with excellent thermal insulation and a very low dead weight. With the UDP, you can ensure the desired floor clearance for patio doors, front doors and windows. The stable, waterproof construction material means that it can be fixed from all sides.
Economical and safe
Details
Installation variant with highly insulating substructure insulating profiles suitable for all door sills and window frames.
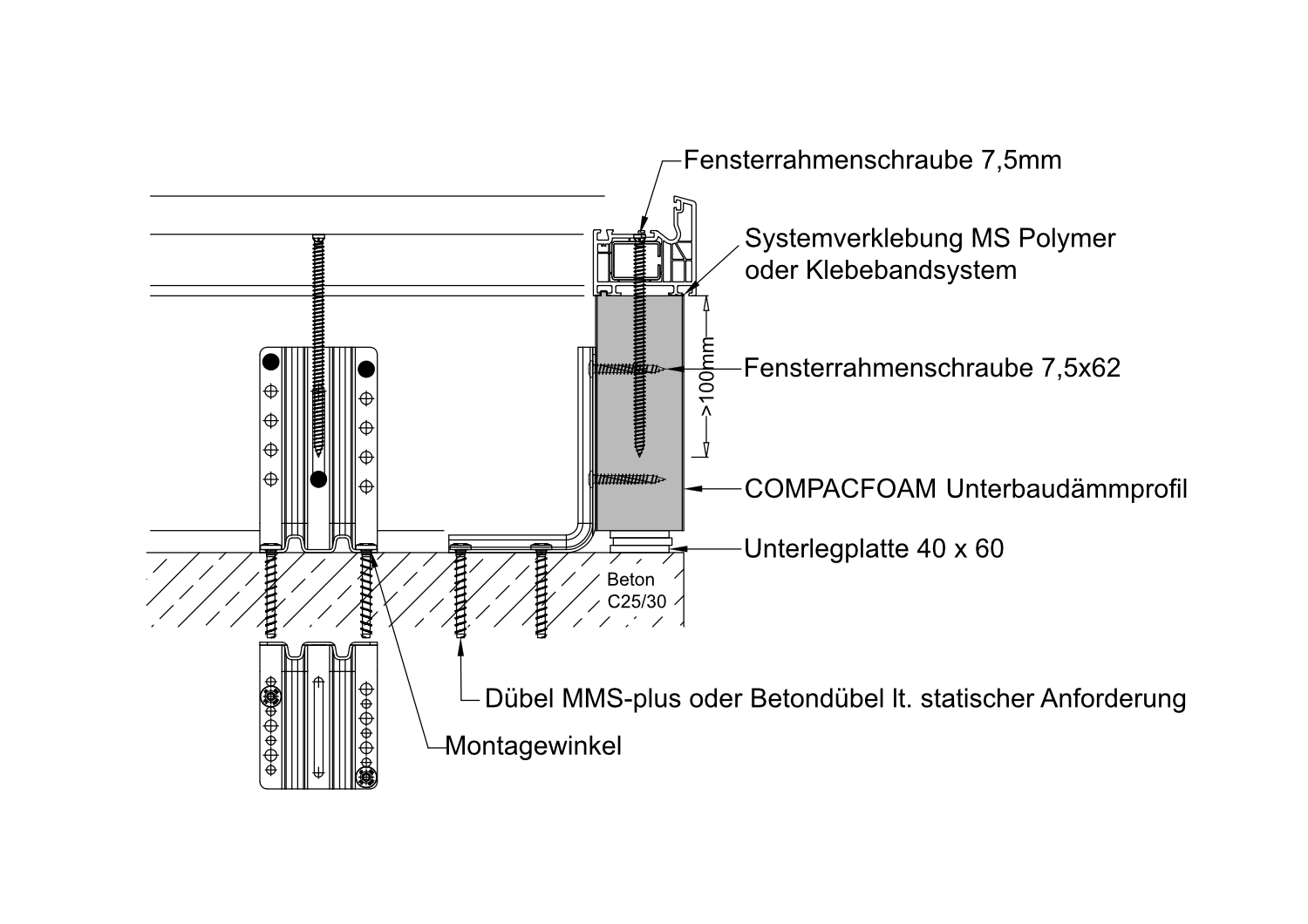
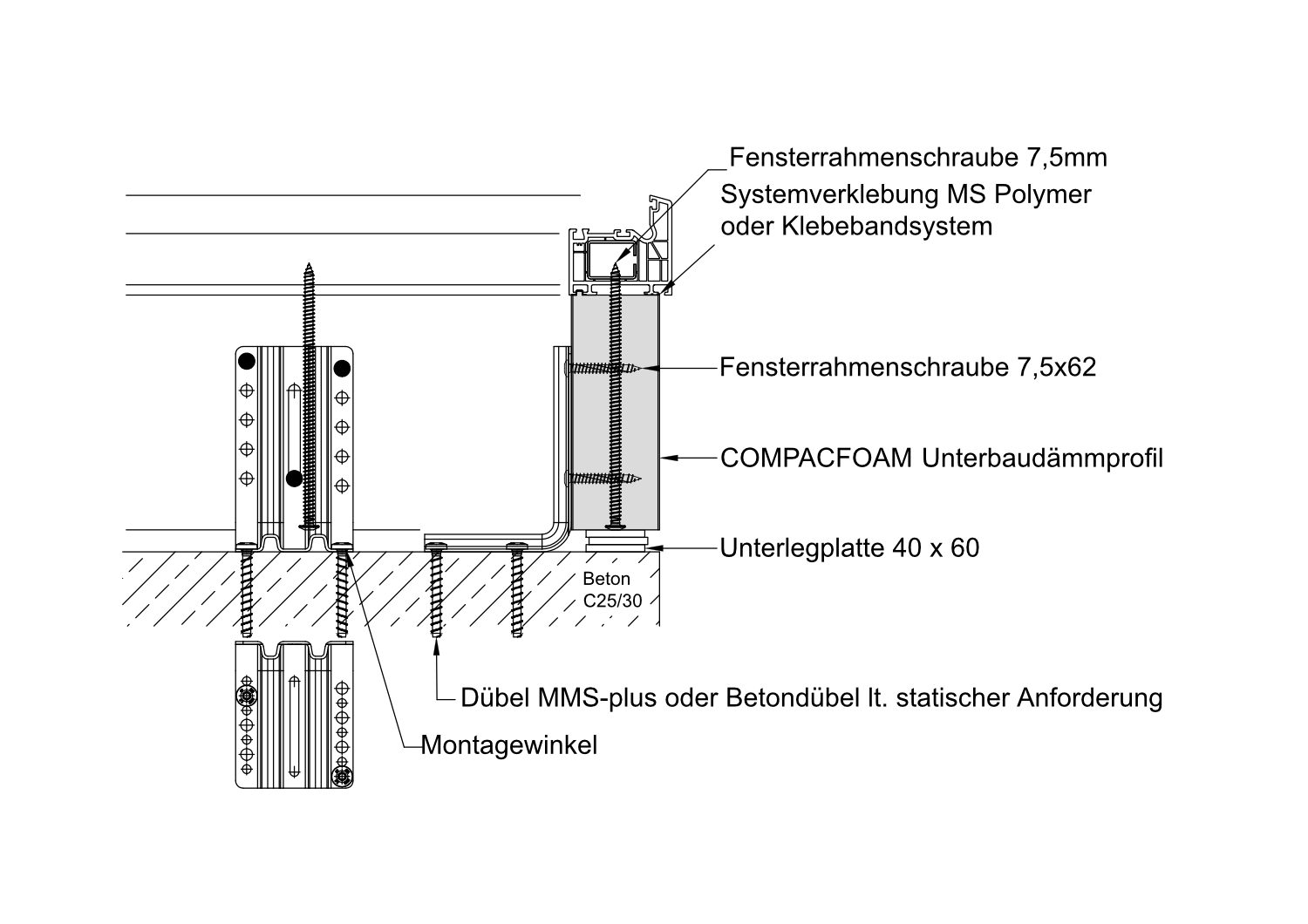
Dimensions:
Surfaces:
Profiling:
A high thermal insulation value is a critical feature of modern substructure insulation profiles. With a lambda value of 0.045 W/mK, CFeco UDPs achieve optimum results here too.
Technical data
* any thickness available
Dimensions
COMPACFOAM Substructure insulation profiles are not only available in the standard length of 2350mm, but also in any desired length up to 6m.
Coating
On request, the substructure can be provided with a PVC coating on one or both sides.
Flexibility
You can achieve maximum flexibility by purchasing panels that you cut and profile yourself in your workshop.
Profiling/contour
There are no limits when it comes to profiling. Individual tools are not absolutely necessary, which allows us to profile even small quantities cost-effectively. We supply the individual substructure for YOUR threshold.
The stacking contour (tongue and groove plug-in connection) allows different stand-off heights to be achieved flexibly.
In addition, processing with our CNC 5-axis milling machine is possible up to 4700x600x300mm in one piece for highly complex and individual requirements.
Examples
The purpose of fall-protection glazing is to protect people from falling to a lower level. They should offer a low risk of injury in the event of an impact and ensure that the traffic area below is not endangered by broken glass. Examples of such glazing include balustrades, glass stair railings and floor-to-ceiling windows. The ETB guideline for fall-proof, floor-to-ceiling components requires a load-bearing capacity of at least 2.8 kN at the relevant fixing points.
The COMPACFOAMsystem fulfills this requirement and thus offers maximum protection and safety with fall-proof elements.
The substructure system must meet the following requirements for verification:
With the COMPACFOAM substructure system, there is an individually tested system for all installation heights up to 240 mm that demonstrably fulfills all requirements.
Complex projects sometimes also require verification of the sound insulation of the substructure profile. Test results are available for various material thicknesses based on EN ISO 10140-2. For increased requirements, superstructures with sound insulation foil on the room side were also tested.
The connection of floor-to-ceiling window and door elements to the adjoining components is one of the most important interfaces of the building envelope. The connection must be made with a waterproof material. Liquid plastics or bitumen membranes are usually used for this purpose. With COMPACFOAM, a secure and permanent connection with liquid plastics and bitumen membranes is possible.
SEALING WITH LIQUID PLASTICS
When waterproofing with liquid plastics, the installer must ensure that a compatible product is used. Under the following link you will find the current list of approved liquid plastics.
All products on the list have been tested for adhesion and compatibility by the manufacturer. If a primer is listed, it must be used!
WATERPROOFING WITH BITUMEN SHEETING
When waterproofing with bitumen membranes using the scarfing method, the installer must ensure that the CF flooring profiles are only scarfed briefly. As a rule, the bitumen membrane is heated on the floor and then rolled onto the CF UDPs while hot and with a liquefied surface. It may be necessary to mechanically press or roll on the membrane to achieve sufficient adhesion. The membrane can then be scarfed over from the outside without damaging the substructure.
As with all materials in reaction to fire class B1, the installer must of course ensure that he avoids direct contact between the building material and the flame in order to prevent the building material from igniting.
COMPACFOAM can be easily cut to size using commercially available saws such as circular saws, pressure beam saws or hand-held circular saws. It is important to use saw blades with a wide tooth spacing and free chip space.
For the cutting of COMPACFOAM we recommend saw blades with flat teeth and chip thickness limiter and very large tooth pitch. Optimum cutting results are achieved at 2000 rpm.
Saw blade recommendation
With the help of a newly developed process, particle technology, we can reduce the waste of COMPACFOAM recycle to 100 %. CFeco200, the result of this process, offers the same good properties as COMPACFOAMhigh strength with excellent thermal insulation.
The COMPACFOAM-substructure insulation profiles are produced in CFeco200 as standard. This means you are using a substructure system that is made from 100 % recycled material. This increases the proportion of recycled material in construction and improves the ecological balance of your project and company. Because environmental protection means keeping things in circulation instead of disposing of them at great expense.
1. air and water tightness
2. pre-assembly
3. installation of the substructure insulation profile
4. installation
5. external sealing
Further information:
Further details on sealing can be found in the "Sealing" data sheet.
To the data sheet